MITCalc - Worm Gear Calculation. Use the Test Creator to design and print. E-PDF Converter and Creator Printer is a PDF printer driver that can be.

The free eMachineShop CAD software includes a spur gear design wizard. Just, fill in the dimensions and select a material. To use the gear design software: • Download the eMachineShop CAD software. • Choose menu File New.
• Select the spur gear wizard. Virtua Tennis 4 Product Key Generator Download. • Enter the desired parameters.
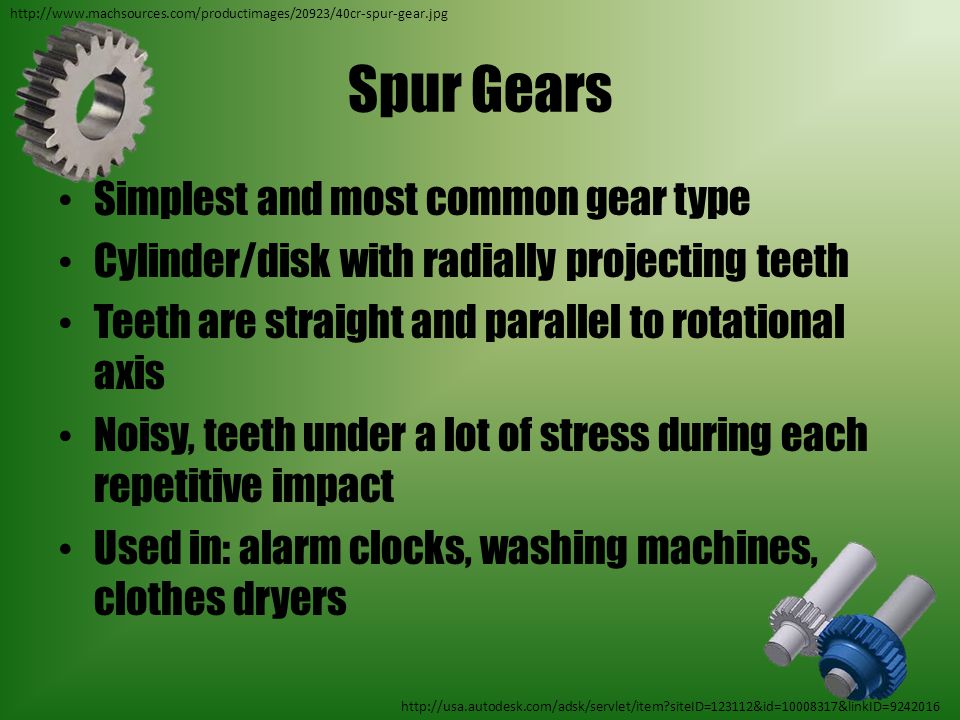
• Add and needed additional features such as a hub or special holes. • Choose Job Material and select a material for your part. • Choose Job Price/Analyze to get feedback on the design. • Choose Order Place Order. Watch the video below.
• On the ribbon, click Design tab Power Transmission panel Spur Gear. • On the Spur Gears Component Generator, Design tab: • Enter the values for the Common section. • In the Gear 1 section, select Feature from the list. The Cylindrical Face and Start plane commands are activated. • In the Autodesk Inventor assembly, select the cylindrical face and start plane. To insert the feature properly, it is necessary to have a user part with sufficient diameter that must be bigger than anticipated Outside Diameter. • In the Gear 2 area, select No Model from the list.
Note: Click More in the right lower corner of the Design tab to open the More Options area, where you can select other options for your calculation. • On the Calculation tab, select Method of Strength Calculation from the drop-down list, and enter values to perform the strength check. Anatomical Automatic Labeling Manual Transfer more. • Click Factors to display a dialog box where you can change factors for selected Method of Strength Calculation. • Click Accuracy to display a dialog box where you can change the accuracy settings. • Click Calculate to perform the calculation.
• Calculation results are displayed in the Results area. The inputs that fail the calculation are displayed in red (their value does not correspond with other inserted values or calculation criteria). Reports of the calculation are displayed in the Summary of Messages area which is displayed after clicking the chevron in the right lower part of the Calculation tab.
• Click Results to display the HTML report with calculated values. • On the ribbon, click Design tab Power Transmission panel Spur Gear. • On the Design tab: • In the Common area, select Center Distance or Total Unit Correction options from the Design Guide drop-down list.
According to your selected option from the drop-down menu, the options are enabled in the Design tab. These two options enable the most logical options to insert your gear model. • Set you desired values, such as Pressure Angle, Helix Angle, or Module. • In the Gear 1 and Gear 2 areas, select Component, Feature or No Model from the drop-down list. Specify numbers of teeth and place the gear set in the assembly, if desired.
• Click More in the right-lower corner to insert more calculation values and criteria. • Click Calculate. Generator designs the gear set model based on entered parameters. • Calculation results are displayed in the Results area. The inputs that fail the calculation are displayed in red (their value does not correspond with other inserted values or calculation criteria).
Reports of the calculation are displayed in the Summary of Messages area which is displayed after clicking the chevron in the right lower part of the Calculation tab. • Click OK to insert the gear set into the assembly.
• On the ribbon, click Design tab Power Transmission panel Spur Gear. • On the Design tab: • In the Common area, select Module and Number of Teeth option from the Design Guide drop-down list. • Enter Desired Gear Ratio and Center Distance values, or select Cylindrical face for both gears in an assembly on position where gearing is placed (Center Distance is measured from Autodesk Inventor assembly). After placement selection of the gearing geometry a preview for gearing displays in the Autodesk Inventor window. • Click Calculate.
Generator designs Module and Number of Teeth. • In the Common area, select Number of Teeth option from the Design Guide drop-down list. Change Module to upper or lower value to decrease or increase Number of Teeth. To decrease or increase number of teeth for first or second gear by one to achieve greater or smaller total unit correction, select Total Unit Correction from the Design Guide drop-down list, change Number of Teeth value, and click Calculate. • On the Calculation tab, enter values to perform the strength check.
• Click Calculate. • Calculation results are displayed in the Results area. The inputs that fail the calculation are displayed in red (their value doesn't correspond with other inserted values or calculation criteria). Reports of the calculation are displayed in the Summary of Messages area which is displayed after clicking the chevron in the right lower part of the Calculation tab.